Retour.
Comment reparer le pont
de son
DC20
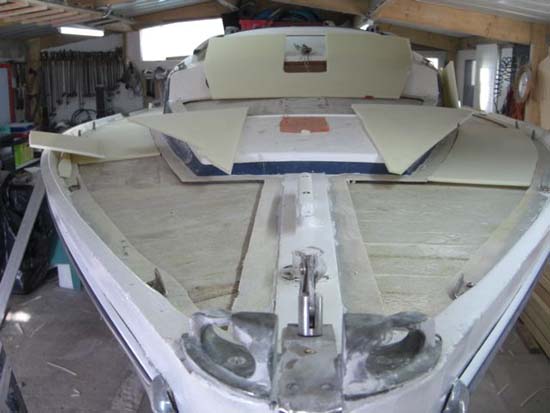
Le pont du DC20 est composé d'un sandwich polyester - balsa - polyester. C'est très costaud et léger tant que l'eau n'y pénètre pas.
Si vous percez votre pont pour positionner de l'accastillage (balcon, rails d'écoute..) prenez grand soin d'ajuster les jonctions et d'étanchéïfier vos percements avant la pose de l'accastillage.
En 50 ans d'usage, les précautions nécessaires n'ont pas toujours été strictement respectées.L'usure fait le reste. L'eau s'insinue dans le sandwich et le pont devient de plus en plus souple jusqu'au moment où il faut intervenir pour redonner au pont toute sa rigidité.
Philippe, Stan et Thierry ont refait le pont de leur bateau. Ces précurseurs qui ont accepté de patager leur expérience, vont vous faire gagner beaucoup de temps car ils ont su
faire preuve d'une réelle pédagogie dans leur récit. A tel point que leurs interventions à coeur
ouvert semblent de nature à gagner les hésitants !
Nicolas a signé une remise à neuf
de son bateau encore plus impressionnante avec une réfection originale du pont
par le dessous.
Les photos en disent plus que les mots. Elles illustrent au mieux les travaux réalisés.
Bonne lecture !
Philippe: Le plastique, c'est fantastique (2019)
La « semaine du golfe » approchait à grands pas et je me décidais de réarmer le bateau. Un petit tour d’horizon me fit remarquer une fissure du plastique autour du mat et plusieurs sur le rouf alors que je savais depuis longtemps que ce toit était par ailleurs très « souple ». Je commençais à soulever la zone fissurée et petit à petit toute la peau est venue. Le délaminage était total et je découvrais un balsa sous-jacent complètement pourri.
Il fallait impérativement s’en occuper car il me restait un mois devant moi avant le rassemblement. Pas question de rater la semaine du golfe!
J’alerte WatsApp Dc20 pour avoir des tuyaux sur la conduite à tenir. Il y avait sur le site les comptes rendu d’expérience de Stan, Thierry et Nicolas mais Pascal Carmier m’a donné tout de suite la méthode et les produits à commander chez Sicomin. Cette entreprise est spécialisée dans ces matériaux et je me suis fait livrer sans difficulté les produits nécessaires à la dose voulue pour la surface en question suivant les conseils de Pascal:
« Bonjour, j'ai remplacé le balsa par de la mousse airex (C70-90 en 6 mm) collée à l'époxy chargée (woodfill 250), puis stratification de 2 tissus biaxiaux (1 de 450g et 1 de 300g) recouverts d'un tissu taffetas de 200g. Le tout avec de l'époxy SR 1500. Tous les produits sont des références Sicomin. J'ai refait ainsi les passavants ainsi que les panneaux avant. Pascal Carmier (Avatar)
Dernière précision, j'ai mis un rectangle de contreplaqué marine sous le pied de mât, en faisant des trous de 14 mm pour les boulons de fixation du pied de mât. J'ai ensuite bouché ces trous à l'époxy chargée puis réservé au diamètre des vis. Cela évite des infiltrations d'eau dans le sandwich. Je procède ainsi pour tous les percements à réaliser sur le bateau (perçage 4mm supérieur à la vis de fixation puis rebouchage à l'époxy puis perçage final au diamètre adéquat) »
Il m’a donc fallu enlever la totalité du balsa pour faire propre en gardant la peau polyester inférieure. J'ai découpé la peau supérieure à la disqueuse en veillant à ne pas aller trop profond pour ne pas découper la peau intérieure. La découpe a été faite en gardant un centimètre sur les bords et le balsa résiduel entre les deux peaux enlevé à la petite curette. Le balsa est très collé par endroit et il faut finir à la ponceuse dure.
Puis prendre des gabarits de découpe en carton à reporter sur le panneau de mousse.
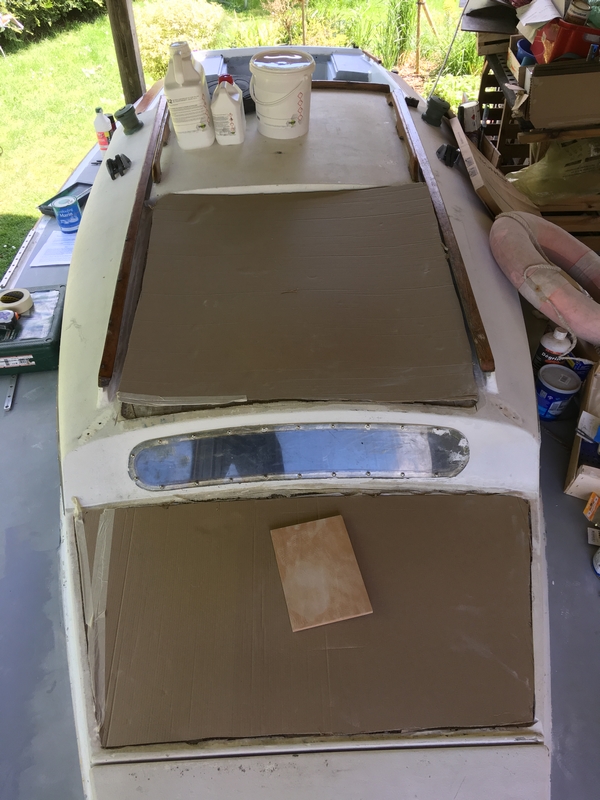
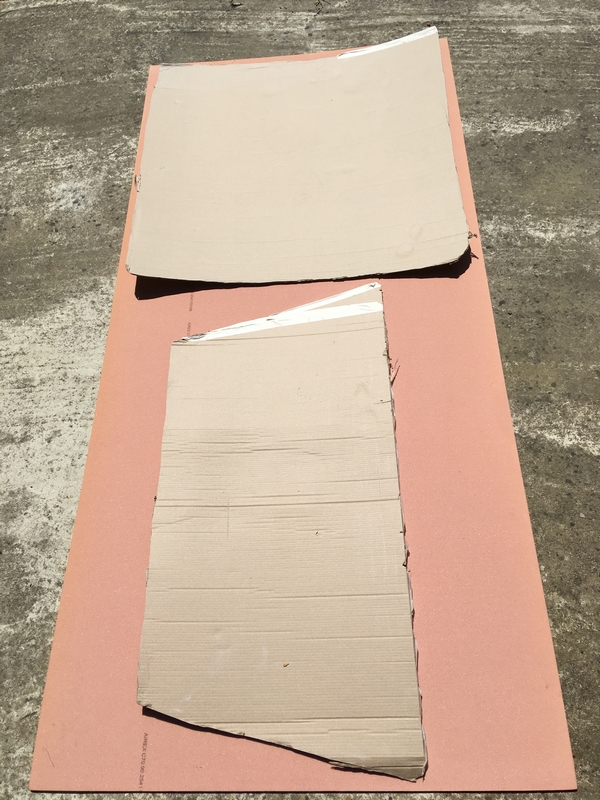
Les panneaux sont présentés pour vérifier leur ajustement.
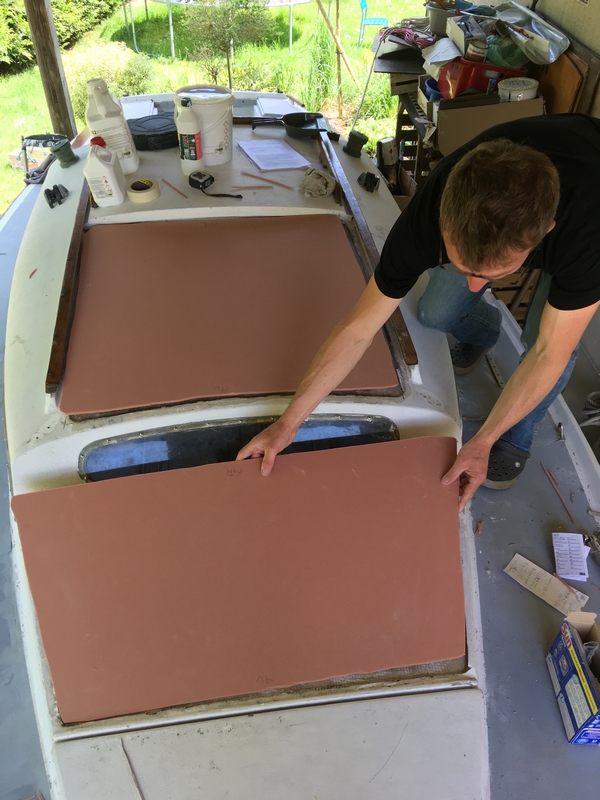
Nettoyage à l’acétone, application de la résine et des panneaux
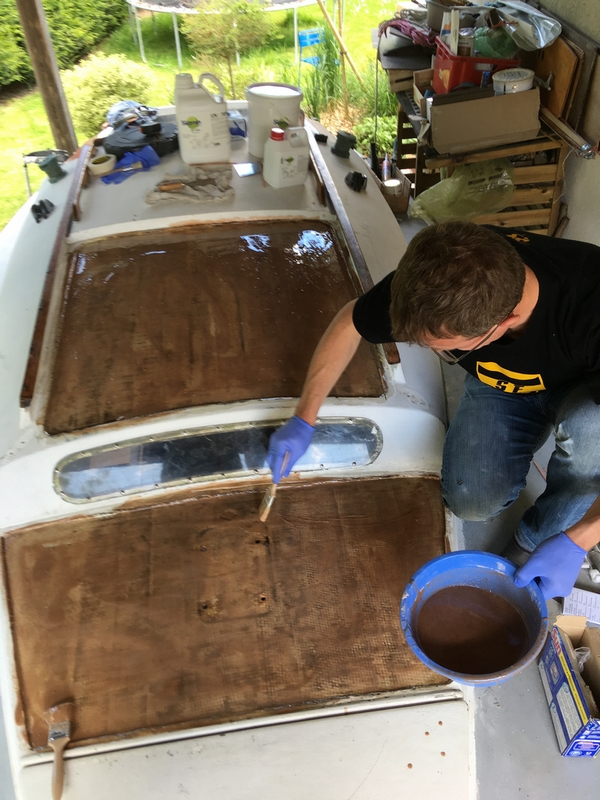
Les panneaux sont ensuite appliqués fortement pour épouser le cintre du rouf.
Là premier gag : Certains pavés ont bénéficié par inadvertance d’un peu de résine ce qu’il faut bien sur éviter. Le décollage après prise a laissé quelques traces que j’ai dû reboucher à l’enduit chargé. Cet enduit est utilisé pour faire les joints « congés ». Ces joints assurent l’étanchéité sur les bords.On voit les traces du décollage des pavés, les cicatrices de celui-ci étant rebouchées au Woodfill chargé. Le tout n’est pas très propre mais c’est solide.
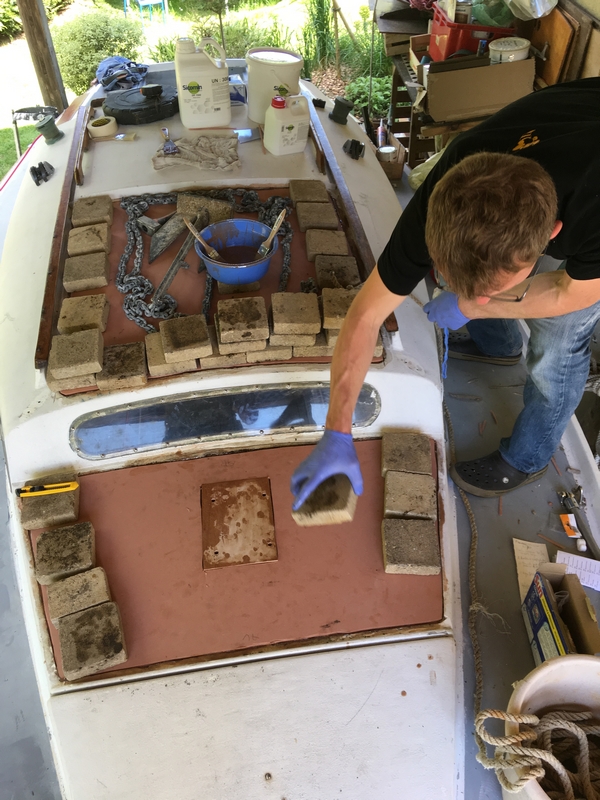
La phase suivante consiste à appliquer les trois couches de tissu de verre collées à l’époxy.
Il est assez difficile d’obtenir une surface rigoureusement lisse même en utilisant le rouleau débulleur. Mon attention avait été attirée par Pascal concernant la température de 18° minimum pour que la colle prenne bien et qu’ensuite cette température ait plutôt tendance à descendre (travailler en fin d’après midi). Malheureusement, le temps pressant, je n’ai pas pu respecter ces conditions et la prise a été aléatoire. Le résultat final laissait un peu à désirer et j’ai dû refaire une couche et reponcer quelque peu.
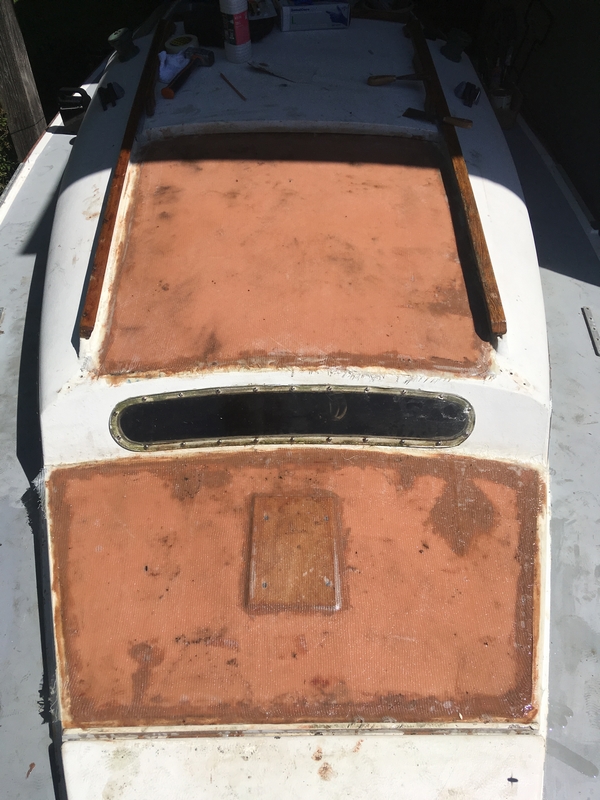
Autre gag auquel je n’étais pas préparé : le rouleau débulleur s’est pris (évidemment) dans la colle époxy en séchant…Non réutilisable. En magasin de bricolage local impossible d’en trouver un autre pour la couche suivante ou d’avoir un conseil utile. Ma seule solution a consisté à mettre le feu à la colle sur un camping gaz et çà a très bien marché.
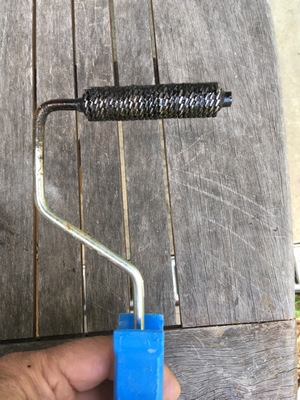 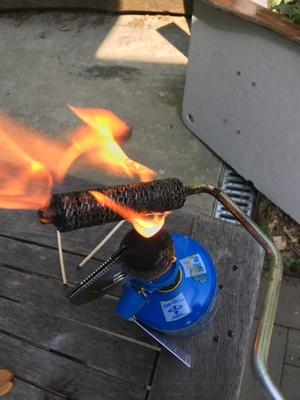
Dernière phase avant la peinture : le gelcoat. Je pensais que ce produit assez épais pouvait un peu masquer les irrégularités de surface. En fait ce ne fut pas vraiment le cas et j’ai du corriger au ponçage.
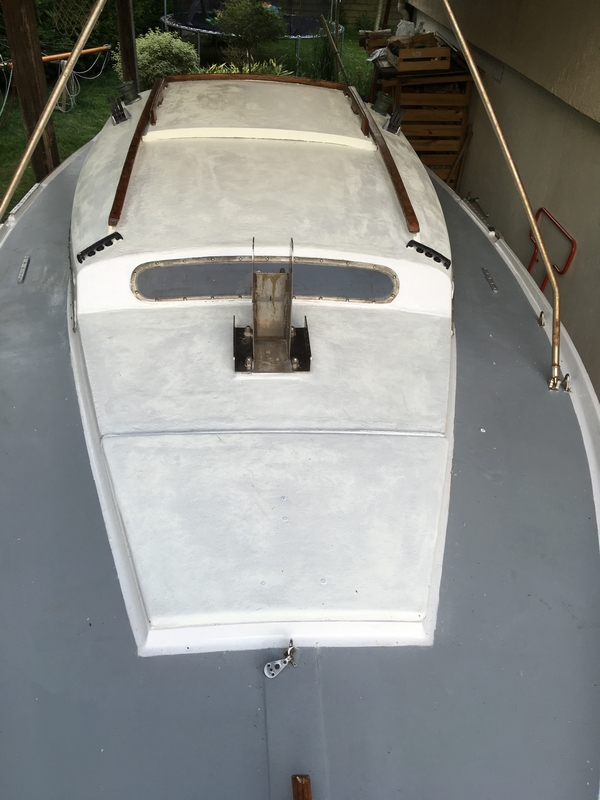
Et voilà : deux jours avant le départ et après une couche de peinture de pont antidérapante le bateau était prêt à prendre la route. Ouf…
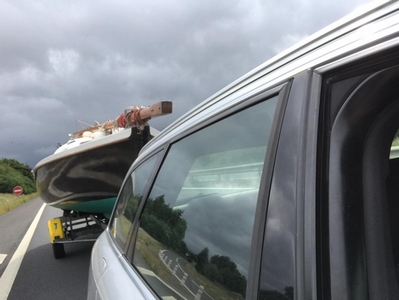 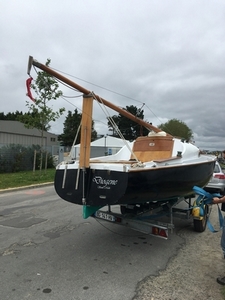
Les deux protagonistes, Charles et Philippe, heureux de leur travail et des belles navigations qui les attendent.
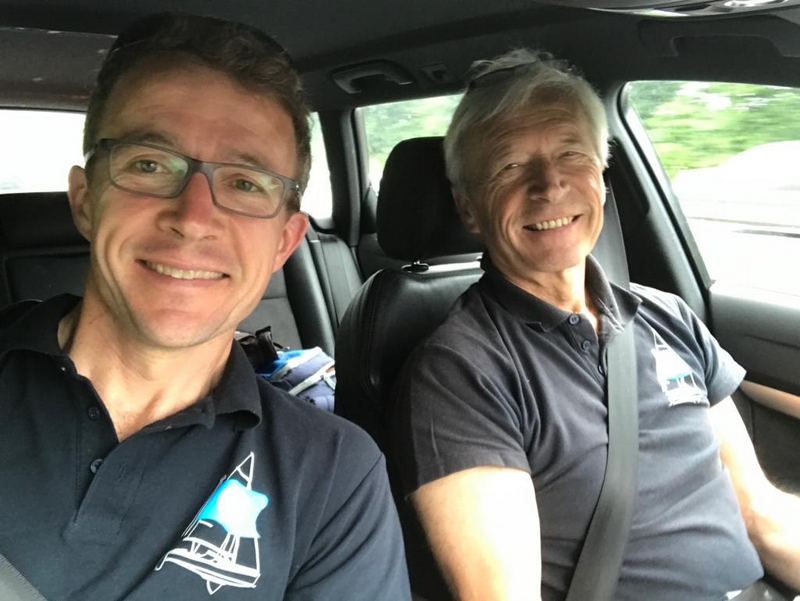
Philippe
Stan:
Nos chers DC20 construit dans les années 60 présentent
souvent des ponts devenus souples au fil des ans à cause
d’un délaminage du sandwich constituant le pont. Cela
rend le déplacement sur le pont désagréable
car on a l’impression que on va passer au travers.
Mon bateau, le n° 86 était atteint d’une manière
très grave de cette maladie et j’ai entrepris de refaire
tout le pont, le dessus du rouf et la zone en forme de trapèze
qui supporte le pied de mât. C’est un travail assez
long mais pas réellement difficile, sous réserve
de procéder méthodiquement et de respecter quelques
règles de base dans la manipulation et l’utilisation
de la résine.
Par choix, j’ai décidé de tout faire en résine époxy,
un peu plus chère que la résine polyester, mais avec
des performances bien meilleures. Le pont de nos bateaux est constitué d’un sandwich
balsa entre deux peaux en stratifié de verre-résine
polyester. Sur mon bateau, le balsa était totalement imprégné d’eau
et totalement décollé de la peau supérieure
ce qui nécessitait son remplacement. Au moment de l’intervention,
j’ai découvert à ma grande surprise que le
balsa était posé de fil et non en « bois
de bout » comme on fait aujourd’hui et cela pourrait
expliquer une des origines de la maladie de nos ponts. Le travail peut être décomposé selon les opérations
suivantes
1)Démonter l’accastillage sur le pont en particulier
les rails de génois et les cadènes de haubans et
les hublots latéraux
2) Poncer intégralement la vieille peinture sur les parois
verticales du rouf et en particulier dans l’arrondi le
reliant au pont (passablement fastidieux car aucune machine ne
peut faire ce travail qui doit être fait entièrement à la
main). Ceci est primordial pour le bon accrochage de la résine
sur lesparties conservées.
3) Découper à la meuleuse la peau supérieure à environ
2 cm du pourtour en faisant bien attention de ne pas entailler
la peau inférieure. Bien prendre ses repères avant
de commencer et tracer avant de découper. Je conseille
de procéder par morceau d’environ 1 m de long au
début afin de bien, prendre la mesure de l’opération.
Enlever la peau supérieure. Dans mon cas, j’ai procédé par
zone, par exemple une longueur de 2 m sur un passavant (voir
photo) avec réfection complète, pour éviter
de se retrouver avec un très gros travail de stratification
ensuite, ce qui pourrait en décourager certains. On perd
certainement du temps, mais cela permet d’étaler
le travail sur plusieurs saisons pour ceux qui n’auraient
ni le temps ni le courage de tout faire en un seul hiver.
Voici
une vue du passavant tribord avec le balsa retiré
.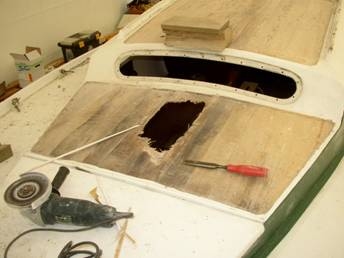
Dans
cette vue, on voit le travail sur le rouf et le pied de mat (il
y avait de quoi faire !!!) et les outils de base : meuleuse
et ciseaux
4) Décoller au ciseau à bois le balsa d’origine
et nettoyer bien tout et passer un bon coup de ponçage à la
meuleuse avec un disque fibre (grain 80) pour retirer les
dernières particules de bois sur la peau inférieure.
5) Re-stratifier un tissu de verre bi-bais de plus ou moins 220
g/m2 sur la peau inférieure pour assurer un renforcement
de celle-ci et assurer une bonne étanchéité pour
le nouveau sandwich ; Ebarber à la meuleuse le tissu
en trop sur les bords.
6) Coller à la résine du balsa « bois
de bout » en 6,4 mm (1/4 de pouce) sur toute la surface à traiter.
Il est difficile de découper le balsa exactement à la
forme demandée et laissé les interstices le long
des bords vides pour le moment. S’assure de bien appliquer
le balsa sur la peau inférieure de façon à obtenir
une bonne adhérence de toute la surface (plus facile à dire
qu’à faire et plus facile sur de petites surfaces
que sur des très grandes!!!). C’est un point clé à ne
pas rater pour la réussite de toute l’opération.
7) Combler les interstices avec de la résine chargée
bien épaisse et lissé le mieux possible avant durcissement.
Meilleur sera le lissage moins il y aura de ponçage
8) Poncer la surface supérieure du sandwich balsa de façon à obtenir
une surface la plus parfaite possible avant la stratification
de la peau supérieure.
9) Stratifier la peau supérieure avec trois tissus de verre
(roving, bibais et taffetas de finition pour un total d’environ
800 à 900 g/m2 ; je me suis efforcé de remonter
les tissus un peu le long des parois du rouf et du petit hiloire
le long du livet et notamment jusqu’au niveau inférieur
des hublots pour renforcer la structure à cet endroit.
Attention astuce de Pro : avec le balsa il est impératif
de travailler en température décroissante au moment
de la stratification ; sans cela l’air contenu dans
la balsa va se dilater en se réchauffant (la résine
dégage toujours une certaine quantité de chaleur à la
polymérisation et vous aller avoir des bulles sous votre
peau. Il faut chauffer l’ensemble auparavant, baisser le
radiateur au moment où on commence à mettre la
résine et éviter les heures le plus chaudes du
début de l’après-midi. Une baisse de quelques
degrés suffit à contrôler la situation et
obtenir une surface excellente.
10) Enduire (mastic époxy)
11) Poncer et peindre selon la couleur de son choix
12) Remonter l’accastillage et les hublots Avec un peu de méthode et d’huile de coude, on s’en
sort très bien. La majorité d’entre nous a
déjà manipulé les résines ou connaît
quelqu’un pour lui donner les premiers rudiments et si on
respecte bien les règles de base pour l’utilisation
de ces produits, on peut obtenir des résultats très
satisfaisants. Le résultat obtenu donne un pont d’une grande rigidité par
rapport à la situation antérieure. Je reste à la disposition de tous ceux qui seraient tentés
de se lancer pour partager mon expérience avec eux.
Cordialement STAN
Refaire
le pont de Roots par Thierry
Je te joints quelques photos de la réfection du
pont de Roots et la méthode. Notre chantier d'hiver est terminé.
Pour récapituler les
travaux: .Outillage : il faut une meuleuse
ponceuse, un cutter, un disque diamant, ciseaux, spatule,
de l'abrasif, un rouleau débuleur. Matériaux : tissu de verre
bibias 300gr, équilibré 3oo
gr, mat de verre gr., mousse de 10mm, 40kg à 50 kg, résine polyester ou
époxy Méthode . 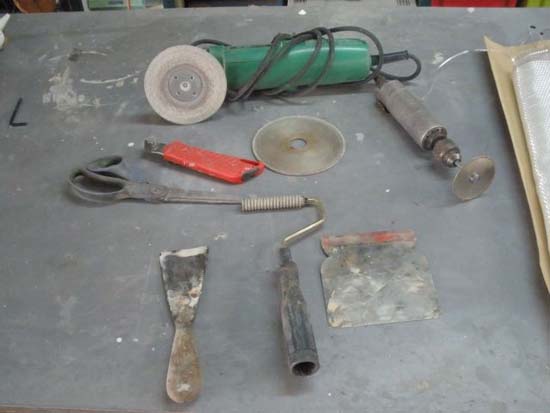
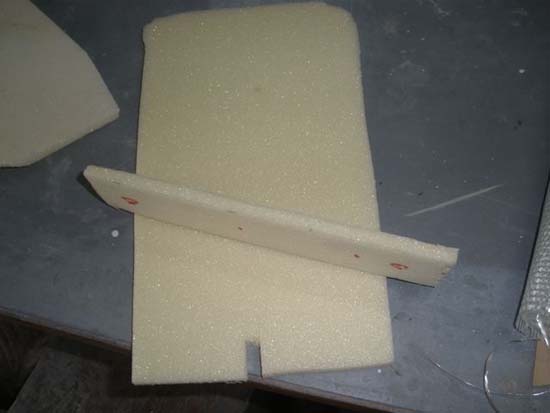
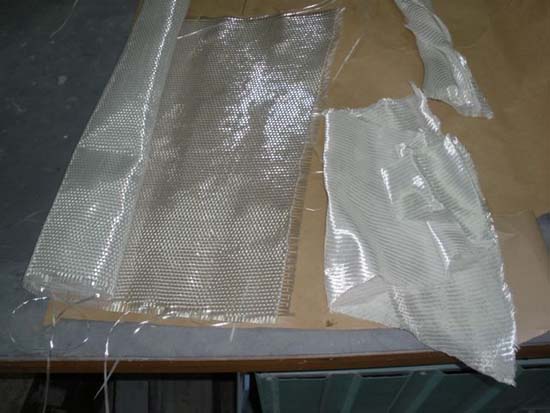
1) Avec la meuleuse et le disque diamant découpé la première peau
du pont en conservant une lèvre de 50
a 60 mm. Ensuite retirer la peau.
2)Dégager le
sandwich balsa et bois et nettoyage de la peau inférieure
3)Si
la peau du dessous est abîmé mettre une couche
de bibias 300g + mat de verre
4) ajuster la mousse et préparer des
inserts pour les parties ou il y a de l'accastillage .Vous pouvez
utiliser l'ancienne peau de verre et faire des empilages coller
ou bien du bois sous les parties ou vous poserez votre accastillage
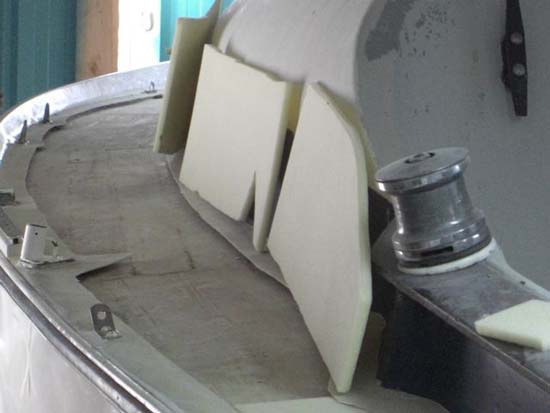
 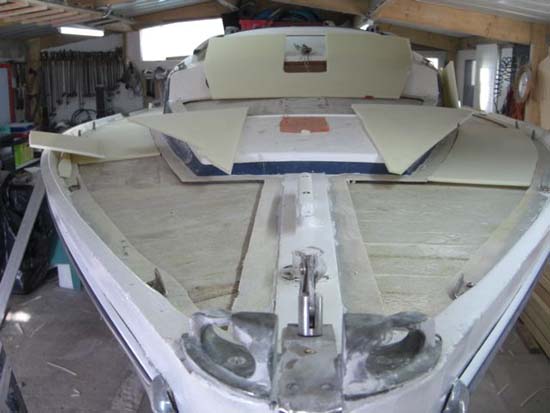
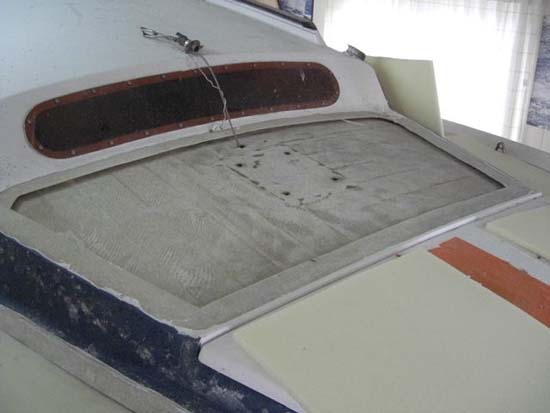
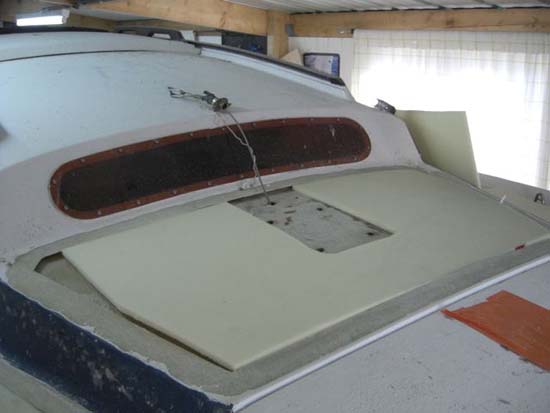
5)
coller la mousse a l'époxy ou polyester en la
chargeant de micro ballon,
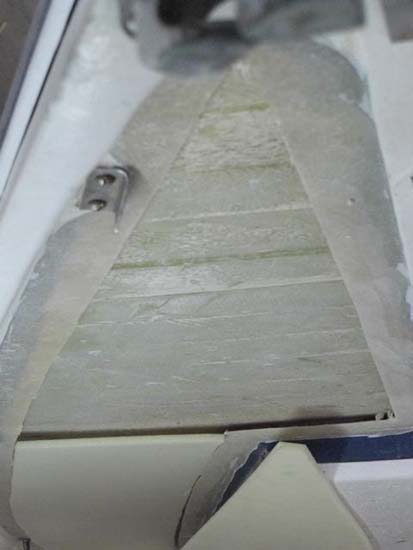
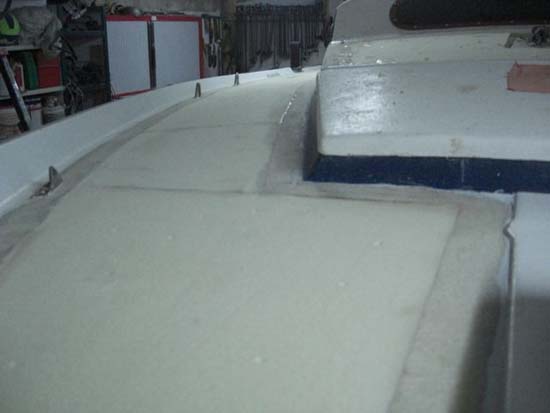 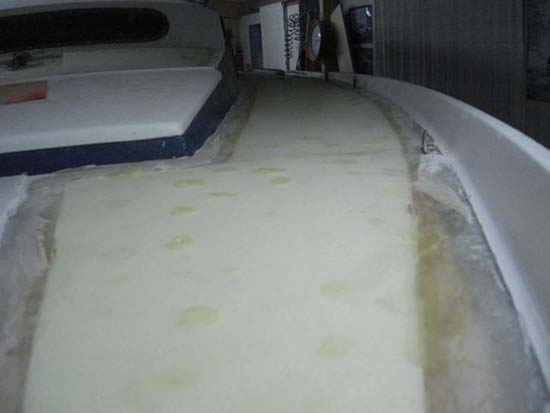
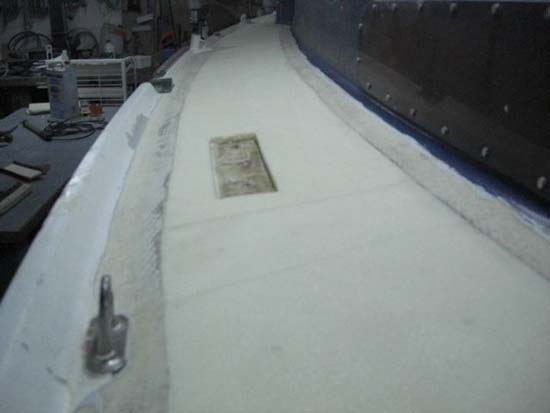 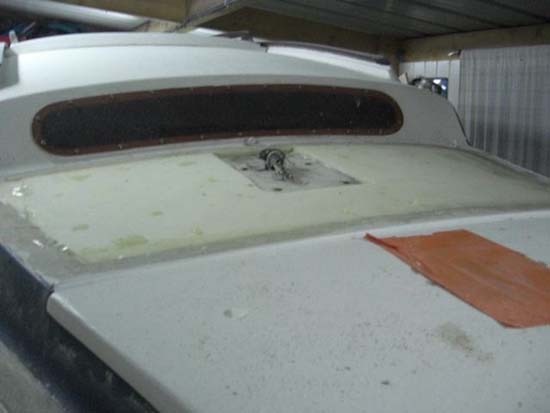 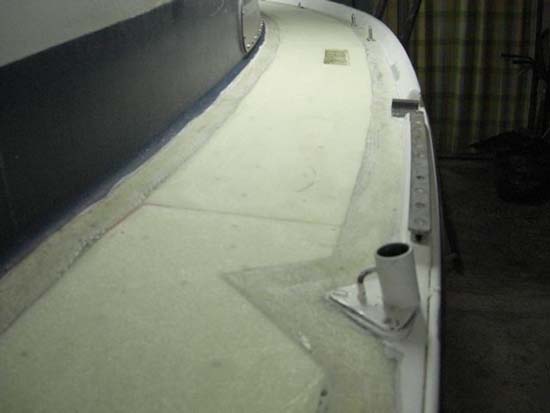 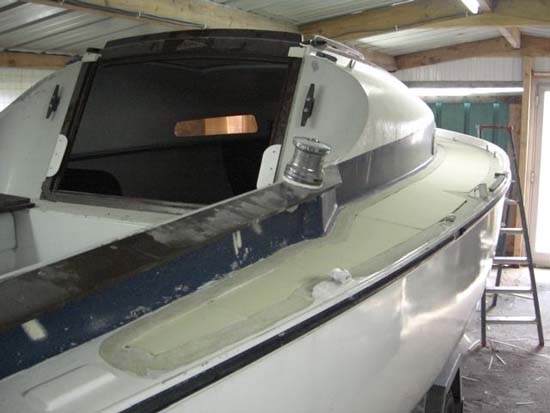 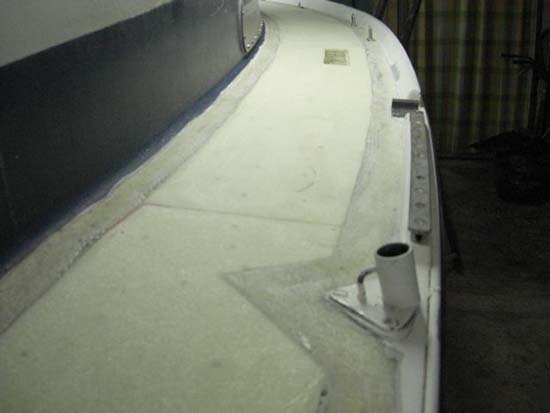 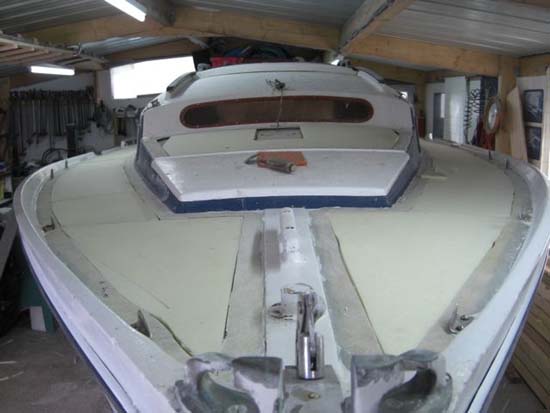
6) Stratification de la peau extérieur 1 bibias 300gr,
1 équilibre 300gr,
1mat 300gr, 1 équilibré
7)finition avec
enduit et résine charge, ponçage calibrage
du pont
8) couche d'après epoxy ponçage grain
fin
9) peinture voici la méthode c'est très simple
a faire il faut juste être un peu méticuleux .
Il faut en gros 7 a 8 journée A vos outils !
et a bientôt sur l'eau !
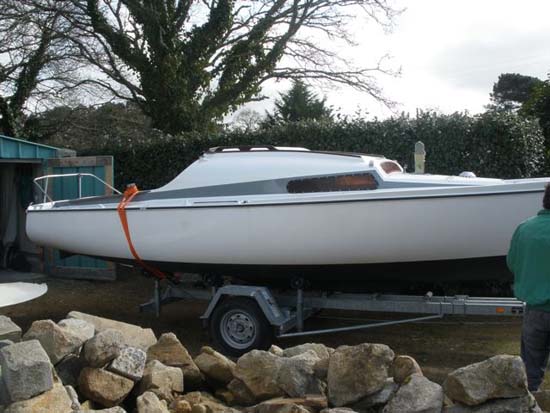
Voilas nous
en sommes là, la suite au prochain épisode,
qui sera stratification et
peinture totale du pont et cockpit.
A vous de jouer !
Tierry
Nicolas
Comme on peut le constater sur les photos
il y avait beaucoup à faire, et les mois de juin et juillet
ont été plus
qu'occupés. Travaillant en extérieur sur une petite
table de jardin, j'ai perdu pas mal de temps à bricoler
des solutions techniques pour palier au manque d'outillage et solutions "ateliers"...
En juillet c'était du 10 heures de travail par jour, puisque
je voulais absolument le mettre à l'eau pour août...
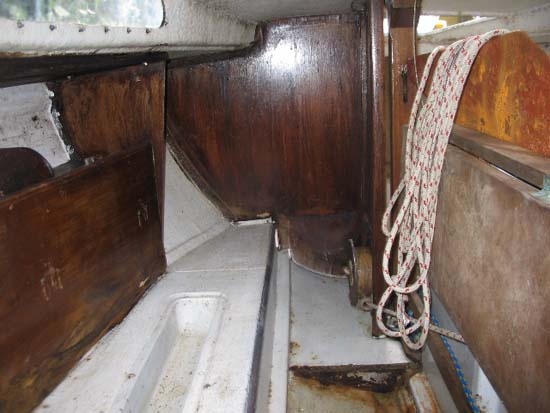
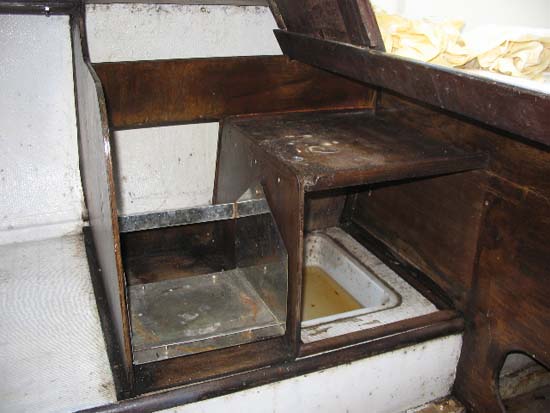
Maintenant il est parfaitement étanche et
solid as a roc !! Le Tubus est un panneau de polyester semi-rigide
constitué de cellules fermées en nid d'abeille, chaque
face de ce panneau est fermé par un voile de polyester prêt à recevoir
une enduction de résine. c'est le meilleur compromis poids/rigidité/prix/mise
en oeuvre. l'effet poutre dû à ce type de matériau
est valable - une fois stratifié- dans les 3 dimensions,
flexion ou torsion, ce qui est un plus pour nos vieilles coque...
La réfection du pont par en dessous est
une opération assez délicate (il ne faut pas entamer
le pont), laborieuse et fatigante (bras constamment en l'air, on
travaille couché sur les bancs dans des positions douloureuses,
on prends toute la poussière de polyester dans les yeux
et le nez malgré les protections) et un peu dangereuse (la
meuleuse au dessus du corps, il ne faut surtout pas la lâcher
!!). Elle à l'avantage de préserver
l'aspect extérieur et de permettre une meilleure finition
intérieure (j'ai fait un joint-congé sur tout le
pourtour intérieur à la jonction coque-pont, c'est
plus net, plus de vis apparentes et plus de recoins qui
s'encrassent un aspect d'ensemble très satisfaisant, comparable
aux constructions actuelles).
La marche à suivre est la suivante : meuler
la peau inférieure en commençant par l'angle pont/roof
en présentant la meuleuse avec un angle de 45°, une
fois que l'on à dégagé une longue portion
on peut y introduire une scie genre" jet cut" à grosses
dents, c'est moins dangereux et plus rapide. Pour l'angle coque/pont
la meuleuse est parfois délicate à utiliser du fait
de son encombrement, dans ces cas là je lui ai préféré une
petite "dremel", c'est plus long (il faut observer de
longues poses pour éviter la surchauffe du moteur) mais
nettement moins dangereux !!! 1
Lorsque l'on à enlevé toute la peau,
il faut raboter toutes les sur-épaisseurs et poncer le futur
plan de joint pont-nidaplast. Ensuite j'ai enduis cette surface
de colle polyester (c'est comme un choucroute mais en beaucoup
plus fin et moins "chewing-gum" plus facile d'emploi
donc), une fois sèche il faut bien sûr la poncer elle
aussi pour être certain d'une bonne adhérence. A ce propos Il faut toujours avoir à l'esprit le
résultat final et sa durée dans le temps, en d'autre
termes ne jamais négliger une phase pour gagner du temps
ou de l'argent au risque certain de perdre les deux au bout du
compte. En d'autres termes les surfaces polyester s'assemblent
sans ponçage quand elles sont "amoureuses" (résine
encore humide). Si l'une ou l'autre est sèche il faut impérativement
la poncer sous peine d'un délaminage futur. Dans mon cas j'ai attentivement préparé la
surface la moins accessible, celle dans le bateau, celle sur laquelle
il est très dur de revenir en cas de galère.
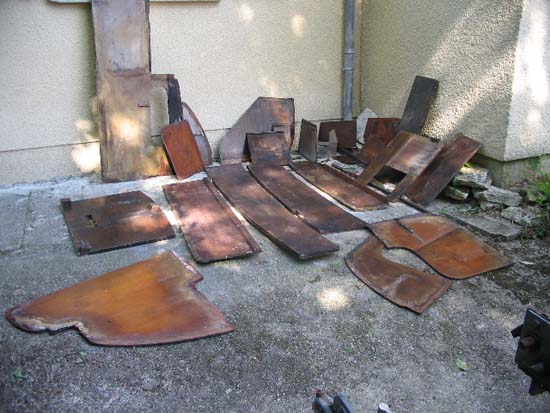 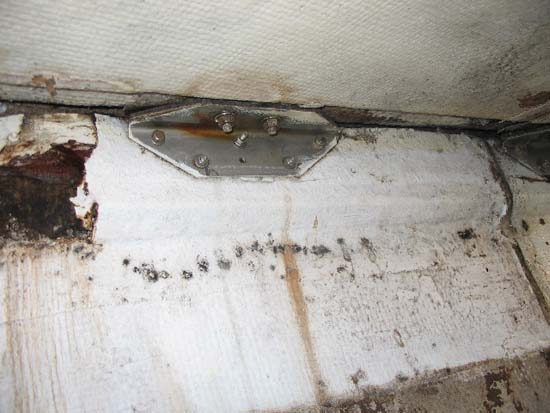 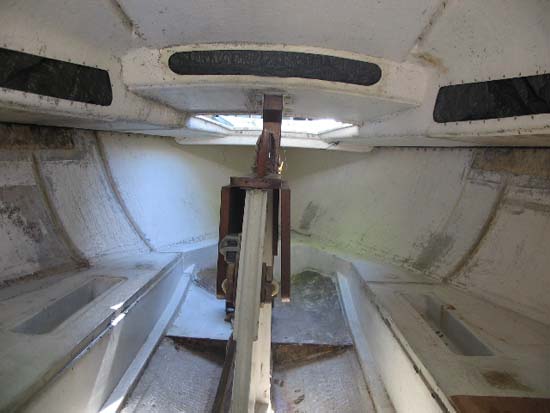
Après avoir impitoyablement enlevé tout
ce qui était en bois j'ai donc refait tout le pont
(des winchs à la pointe avant) par en dessous (c'est à dire
de l'intérieur) en Nidaplast (ou Tubus : cellules en nid
d'abeille de polyester)+ roving+ résine
. 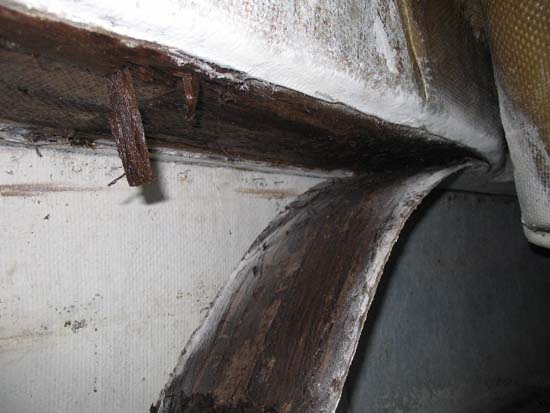
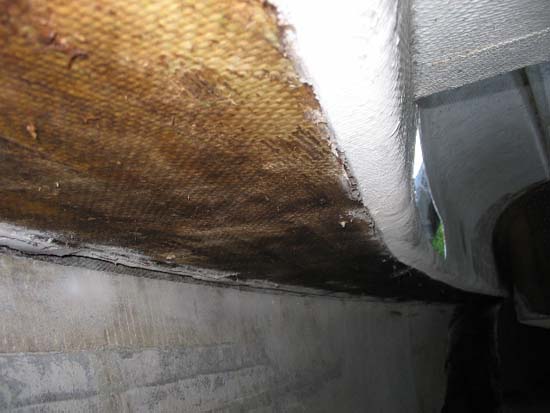
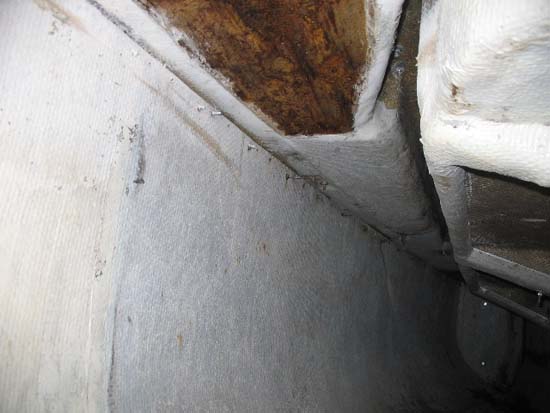
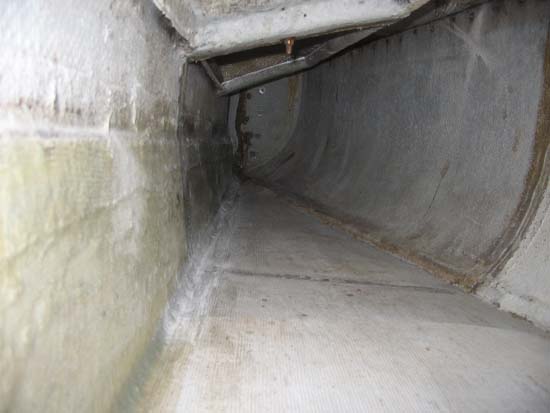
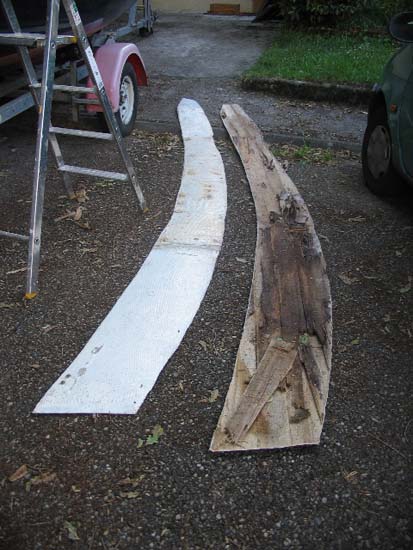
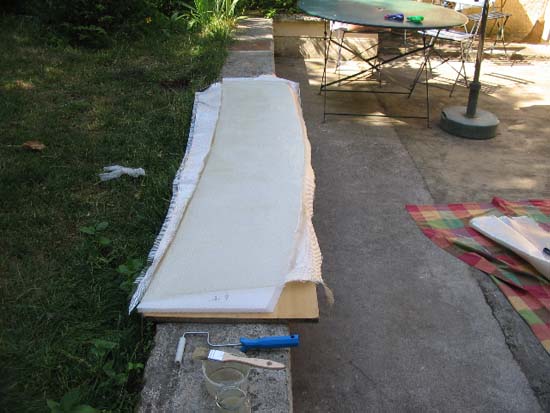
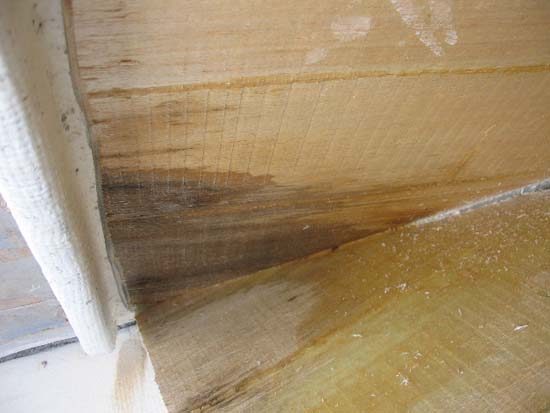
Quand le pont est prêt à recevoir
le nidaplast (épaisseur 15mm) c'est à dire quand
on à bien vérifié qu'il n'y a plus de défauts
de planéïté, on beurre généreusement
le Tubus de colle polyester, on le présente sous le pont
et on le plaque avec des étais préalablement coupés à la
bonne longueur. Quand ça dégueule à peu près
partout c'est que c'est bon... Avant ça bien évidement on a fait
des gabarits grossiers en cartons d'emballage, puis on à affiné ces
gabarits sur un carton rigide de 3mm pour tracer les futurs
passavants à coller. Pour ces pieces je me suis contenté de stratifier
seulement la sous face (résine+ roving 300g).
Quand cette
face est bien sèche (après 2/3 heures), la face interne
(celle qui va coller au plafond!) est juste enduite de résine
et quand celle-ci est amoureuse ( elle commence à polymériser)
je l'enduis généreusement de colle et plaque le tout
sous le pont lui même enduit de résine amoureuse.
Pour récapituler, on à donc dans
l'ordre et partant du dessus :la peau du pont proprement dit, une
couche de résine après préparation (ponçage),
une couche de colle polyester (poncée), une couche de résine
l'ensemble forme la nouvelle peau extérieure sous laquelle
on a :une couche de colle polyester, une couche de résine,
le Tubus (ou Nidaplast), une couche de résine et enfin le
roving 300g qui sera poncé avant de recevoir 2 couches de
gelcoat blanc ... voilà, voilà, voilà...
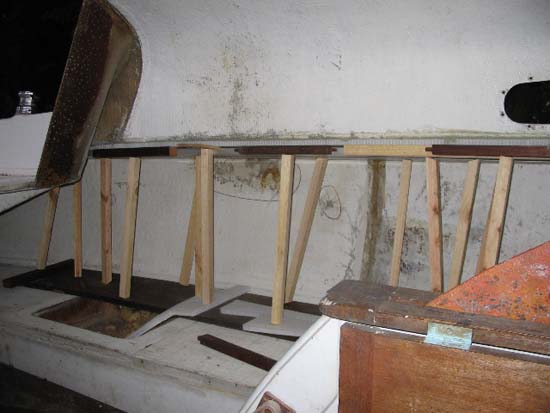
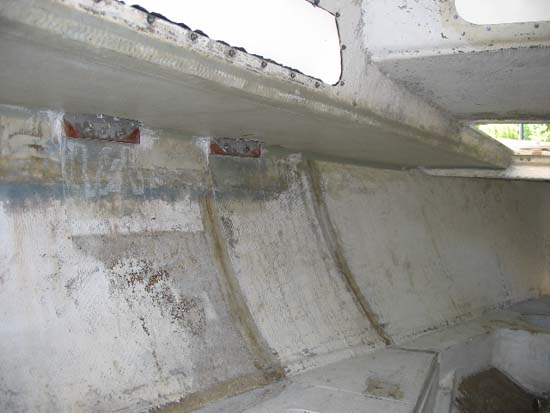
Pour le reste, j'ai refait tous les aménagements
intérieurs en profitant de l'occasion pour les modifier, compte
tenu que mon coffre bâbord près de la descente avait été condamné probablement
dès l'origine, peut-être à la demande du 1er
propriétaire. Du coup j'ai installé les deux couchettes
en vis-a-vis et des rangements simples sous forme d'étagères,
le tout bien sûr en cp marine. Je n'ai pas reproduit le style dc20 qui à mon
sens n'offrait pas assez de surfaces de rangement et à l'inverse
offrait trop de recoins impossibles à nettoyer et surveiller. Il est vrai que l'ensemble manque un peu de la
poésie des lignes courbes et je comprendrais que l'on conteste
mon choix. Néanmoins c'est plus joli en "vrai" qu'en
photos... Pour les coffres j'ai stratifié la face
intérieur coté cockpit qui était en contreplaqué nu,
j'ai refait les séparation en Tubus collés par joint-congés
et passé un gel coat partout. c'est maintenant solide et
parfaitement étanche. j'en ai profité pour caler
en force sous le cockpit une mousse de polystirène neuve
qui lui redonne de la rigidité.
Comme tous les éléments
en bois extérieurs étaient à refaire, les
nouveaux sont maintenant en acacia (sauf la barre d'écoute qui reste à faire,
le temps m'a quand même manqué pour tout mener à bien).
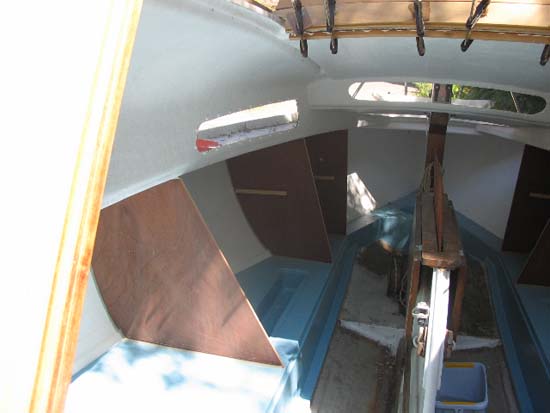
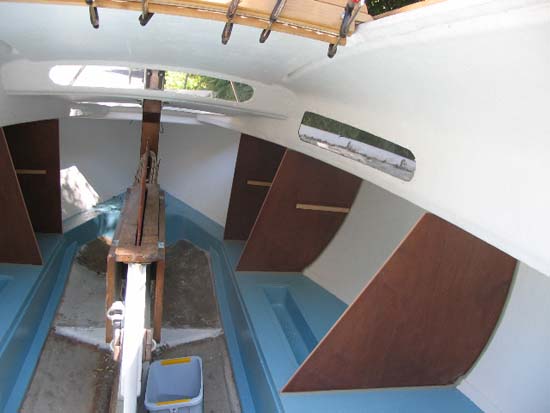
Tu remarqueras aussi que j'ai légèrement
modifié l'entrée en la réduisant de qq centimètres,pour
ma part je la trouve ainsi plus élégante, la porte
se range + facilement et on peut s'adosser au roof de manière
nettement plus confortable...Pour façonner les hublots je
recommande la meuleuse avec laquelle on peut à la fois couper et "poncer" les
bords et les angles... c'est plus facile et efficace que la scie
sauteuse, rabots et autres limes... Dans mon bateau la mousse des coffres était
pleine d'eau, j'ai dû découper les petits équipets
du dessus, percer des trous d'évacuation en partie basse
et les faire sécher pendant 2 mois avant que la mousse ne
redevienne sèche et dure. je pense qu'il devait y avoir
une belle surcharge... Les renforts (ou cales en bois) des cadènes,
bien cachés par le polyester étaient complètement
pourris, j'invite chacun à y aller voir, si je n'avais pas
dû refaire le pont, j'aurais probablement laissé cette
partie là en état... et démâté cet été...
(petit coup de vent bien sec).
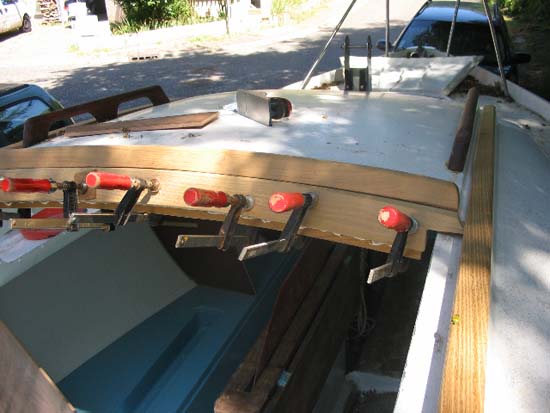
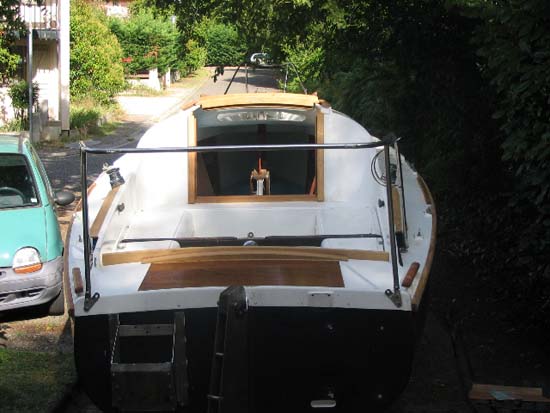
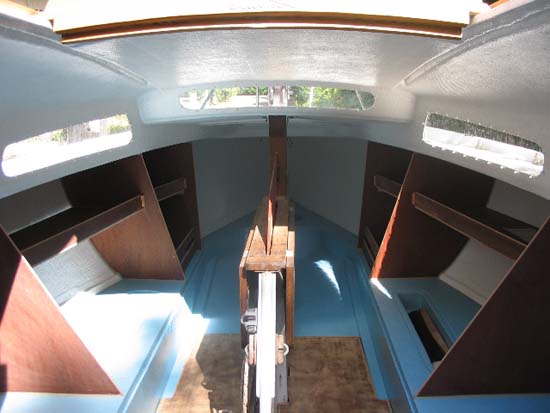
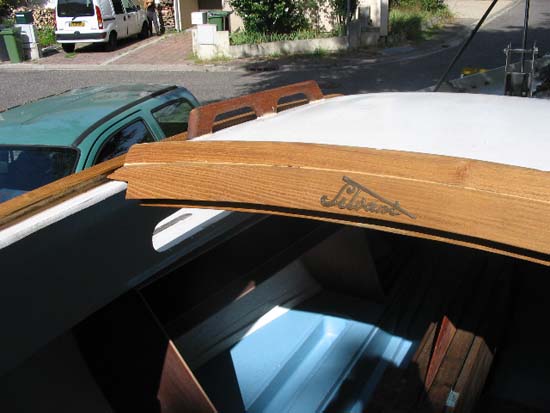
Pour éviter l'humidité, la coque
est entièrement ouverte : les cloisons des coffres et les
cloisons coffre/cabine (en Nidaplast elles aussi) ne montent pas
jusqu'au pont de sorte que l'air circule, j'ai percé et
installé deux aérateurs sous le pontage arrière,
l'avant est ouvert au niveau de l'écubier, je prévois
d'installer un aérateur sur le panneau du trou d'homme.
pour la même raison les aménagements sont les plus
simples possible, pas de recoin-nid-à-moisissure.
Mon regret : n'avoir pas eu le temps de m'attaquer
au pontage du mat, sinon je lui aurais appliqué la même
méthode, comme il est étanche ce n'était
pas une priorité. Pour rigidifier le roof un peu souple, je pense
que deux petits longerons intérieur en bois ou en omégas
de polyester suivant les rails du panneau coulissant devraient
suffire. La saison prochaine je me pencherais sur l'accastillage
du mat et de la bôme et je réfléchirais à un
safran moins lourd et plus pratique de manoeuvre, le bout pour
descendre la pelle ayant une fâcheuse tendance à se
coincer.
Voilà, j'espère n'avoir pas été trop
long, confus, péremptoire ou prétentieux si mon expérience peut servir à d'autre
ce sera avec plaisir. A bientôt sur la toile.
Nicolas
|